Mechanical, Chemical & Wear Testing
Tested, verified and proven
Matrix provides specialised mechanical, chemical and wear testing to validate the performance of products used in some of the world’s harshest environments. From deepwater buoyancy modules to high-wear mining components and defence equipment, our in-house test facilities replicate real-world loads, pressures and exposures. This ensures every product we deliver meets the highest standards for safety, durability and reliability.
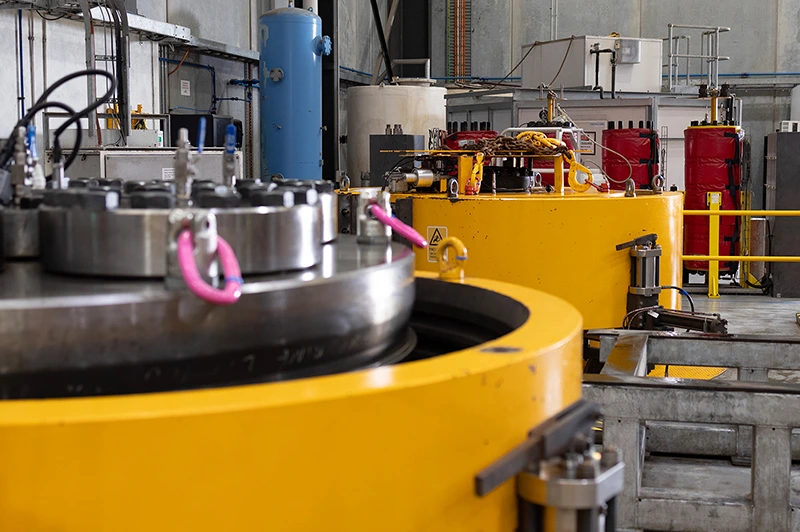
Mechanical, Chemical & Wear Testing
Tested, verified and proven
Matrix provides specialised mechanical, chemical and wear testing to validate the performance of products used in some of the world’s harshest environments. From deepwater buoyancy modules to high-wear mining components and defence equipment, our in-house test facilities replicate real-world loads, pressures and exposures. This ensures every product we deliver meets the highest standards for safety, durability and reliability.
PURPOSE BUILT TESTING FOR PROVEN FIELD PERFORMANCE
Our testing capability is fully integrated into our engineering and manufacturing operations in Western Australia – home to the world’s largest syntactic foam manufacturing plant. We support product development across the subsea, energy, mining, defence and infrastructure sectors with rigorous, real-world performance validation.
We conduct mechanical testing of distributed buoyancy module clamps, hydrostatic and hyperbaric testing of full buoyancy modules and long-term wear testing of centralisers to simulate the in-field conditions in deepwater, high-pressure and high-friction environments. Our fatigue testing programs ensure long-term structural integrity, while chemical exposure validation processes assess material compatibility with aggressive fluids, oils, and process chemicals.
Southern Hemisphere’s largest hyperbaric test facility
Our Subsea Test Centre in Henderson is the Southern Hemisphere’s largest commercially available hyperbaric test facility, with 11 chambers ranging up to Ø1.6 x 6.4 m (5,200 m sea water equivalent). The centre supports functional testing under pressure, with real-time data capture for pressure, temperature, and buoyancy loss.
The Centre is also home to Australia’s first Hyperbaric Common User Facility (HCUF), developed in collaboration with the Western Australian Government, SICA, and Baker Hughes. The HCUF provides open access to high-pressure testing infrastructure, enabling local and international operators to validate subsea technologies to the highest industry standards.
Comprehensive infrastructure for end-to-end testing
Our mechanical and lab testing capabilities also include tensile, compression, shear, dropped-weight impact, fatigue analysis and paint adhesion analysis. We also conduct advanced material characterisation using DSC, TGA, pycnometry, alongside long-term seawater and creep evaluation. All testing is conducted to ASTM, ISO, and API standards, with third-party witnessing available.
OUR TESTING CAPABILITIES
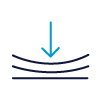
Mechanical Testing
Tensile, compressive, and flexural testing for clamps, modules, and composite components.
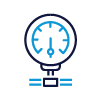
Hyperbaric Testing
Deepwater pressure simultation to validate structural and sealing integrity under load.
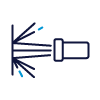
Wear Testing
Abrasion and cyclic wear testing for long-term durability in critical components.
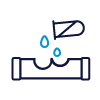
Chemical Resistance
Exposure testing to acids, solvents, hydrocarbons, and process fluids.
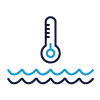
Thermal Simulation
Thermal cycling, heat aging, and moisture conditioning to validate environment readiness.
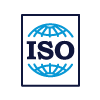
Compliance and Verification
Testing to ASTM/ISO standards with optional third-party witnessing.
SUBSCRIBE
Subscribe
"*" indicates required fields