CARBON FIBRE COMPOSITES
LIGHTWEIGHT STRUCTURAL PRODUCTS FOR THE RESOURCES SECTOR
WHAT ARE CARBON FIBRE COMPOSITES?
Carbon fibre composites rely upon blending reinforcement fibres with a liquid resin. The fibres are often woven into a fabric or otherwise assembled to maintain control over their orientation and the thickness of a single layer. This ‘fibre architecture’ will become the core of the design, and is tailored to efficiently distribute the loads through the structure.
Once the final configuration has been achieved, the resin is allowed harden. For the majority of laminates, a thermoset resin is selected, providing an initial low viscosity liquid that is later crosslinked into an amorphous polymer network to lock the reinforcement in place.
KEY BENEFITS
The unique properties of carbon fibre composites provide significant benefits over traditional materials.
- High stiffness and strength – carbon fibre is less likely to wear and suffer from fatigue than other alternatives and will not degrade in poor environmental conditions.
- Lightweight – carbon fiber is lighter than other traditional materials such as steel and aluminum.
- Corrosion resistance – carbon and the accompanying resin are very stable and non-reactive, making carbon fibre an ideal replacement for steel and concrete in corrosive environments.
- Low CTE (Coefficient of Thermal Expansion) – carbon fibre can easily deal with thermal stress as it has nearly zero heat expansion.
- Highly flexible – carbon fibre can be easily manipulated to manufacture shapes of all sizes and materials unlike steel alternatives.
APPLICATIONS
Carbon fibre composites are used by Matrix to enhance durability and improve the life span of key infrastructure and company assets. Carbon fibre composites provide unparalleled protection and can be used in a variety of situations including:
MANUFACTURING PROCESSES
Matrix deploys a range of manufacturing processes to create smarter solutions which are lighter, stronger and safer:
HAND LAYUP
This is the composite moulding process most people are familiar with. The dry reinforcement is ‘wetted out’ with the liquid resin to create a thin composite shell matching the geometry of the underlying tool. If this sounds similar to the papier-mâché you remember in primary school, you would be correct. Papier-mâché is a wood fibre composite, bound together with wallpaper paste.
At Matrix, hand layup is a useful stepping stone when optimising a part, providing a hands-on practical understanding of the geometry that can be used when designing more sophisticate processes.
VACUUM INFUSION
Although hand layup is simple, the fibre volume fraction that can be achieved is limited. The fibre reinforcement will do the work in the final part, so for a given geometry maximising the fibre and minimising the binder will produce the optimal material properties.
At Matrix, vacuum infusion seals the fibre architecture within a flexible vacuum bag, compressing the stack and minimising spaces between filaments. We then infuse liquid resin into these spaces, bonding the fibres together and creating the final part.
RESIN TRANSFER MOULDING (RTM)
Both hand layup and vacuum infusion typically work on a single surface mould tool. The non-moulded surface, therefore, is often poorly defined and lacks a good surface finish. This is a particular issue when the parts are not simple shells but require three-dimensional form and volume.
In contrast, RTM occurs within a closed tool and the entire outer surface of the part is controlled. The tool is initially filled with reinforcements – both particulate and continuous fibre – and the interstitial spaces filled with the liquid resin. Whenever possible, this final process is carried out under vacuum to minimise the chance for air pockets to weaken moulding.
At Matrix, the RTM process has also been substantially automated, keeping staff out of harm’s way and allowing them to focus on optimising the quality of the final part.
TRIMMING AND FINISHING
Often overlooked, the trimming and finishing of the moulding can be as complicated as the moulding process itself.
Matrix employ a range of manual, semi-automated and fully automated techniques to transform the freshly moulded part into the finished item, ready for service.
VERIFICATION AND VALIDATION
With many of our products forming part of a critical piece of infrastructure, our clients need to be assured that we have both built the right thing and built it right.
Matrix continually invest in new capability to ensure the properties our customers care about are properly monitored, such as acoustic wave speed and hydrostatic performance. For example, Matrix have built the southern hemisphere’s largest deep water simulation facility, with hyperbaric chambers capable of achieving sea water depths of 6 750 m.
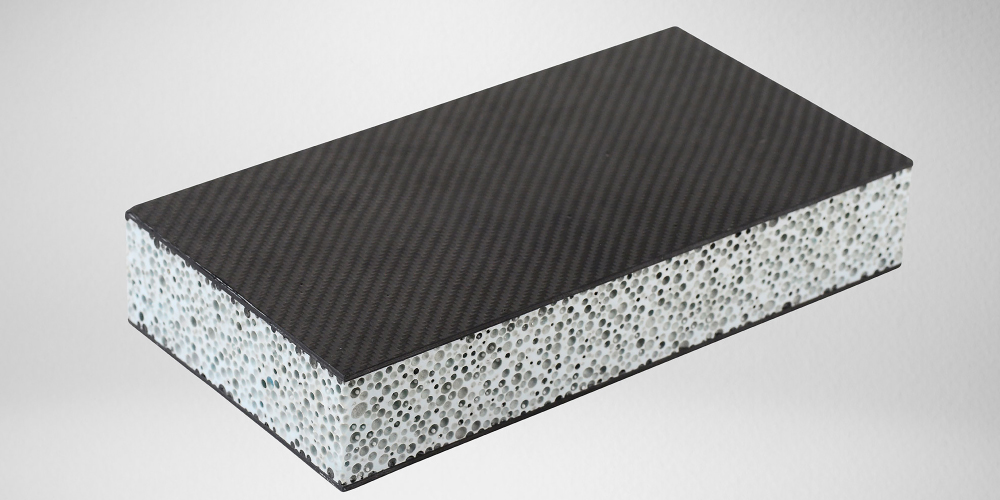